Expert Strategies for Preventing Weld Undercut Successfully
Grasping the Art of Welding: How to Stay Clear Of Undercut Welding Issues for Flawless Manufacture Results
By recognizing the origin triggers of undercut welding and carrying out efficient strategies to avoid it, welders can raise their craft to brand-new degrees of excellence. In the pursuit of remarkable manufacture outcomes, understanding the art of welding to stay clear of undercut problems is not simply an ability yet a need for those striving for perfection in their job.
Recognizing Undercut Welding
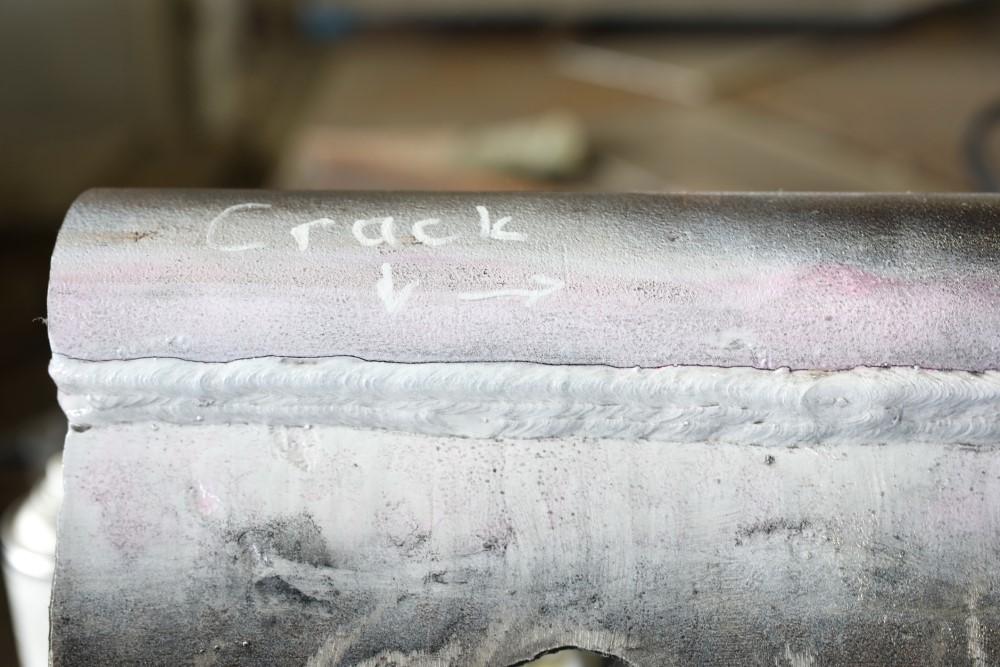
To stop undercut welding, welders need to make sure proper welding parameters, such as adjusting the existing, voltage, travel speed, and preserving the right electrode angle. Additionally, making use of the appropriate welding method for the specific joint arrangement is important. Employing weaving motions or backstepping techniques can aid make sure correct weld steel deposition and minimize the possibility of undercut development. Normal assessment of welds during and after the welding procedure is also vital to capture any kind of undercut very early and make required changes to stop more issues. Preventing weld undercut. By comprehending the root causes of undercut welding and implementing safety nets, welders can attain top notch, structurally audio welds.
Reasons For Undercut in Welding
Comprehending the variables that add to undercut in welding is crucial for welders to produce top notch, structurally audio welds. Inadequate welding inaccurate or existing welding speed can also contribute to damage. Comprehending these reasons and implementing correct welding techniques can aid avoid undercutting problems, making certain solid and long lasting welds.
Strategies to Stop Undercutting

To reduce the danger of damaging in welding, welders can employ strategic welding methods focused on enhancing the quality and honesty of the weld joints. One efficient method is to adjust the welding criteria, such as voltage, current, and take a trip rate, to ensure correct warm input and deposition. Preserving an ideal electrode angle and ensuring consistent travel speed can additionally help stop undercut. In addition, using the correct welding strategy for the particular joint arrangement, such as weave or stringer beads, can contribute to reducing damaging. Preventing weld undercut.
In addition, proper joint prep work, consisting of making certain clean base products totally free of pollutants and making use of the proper welding consumables, is essential in avoiding undercut flaws. Employing back-step welding strategies and controlling the weld bead account can additionally assist disperse warmth evenly and decrease the threat of undercut. Normal examination of the weld joint throughout and after welding, as view it well as executing top quality guarantee actions, can aid in resolving and identifying undercutting problems quickly. By carrying out these techniques faithfully, welders can achieve flawless manufacture results with minimal undercut flaws.
Significance of Correct Welding Specifications
Picking and maintaining ideal welding parameters is necessary for achieving successful welds with very little problems. Welding parameters describe variables such as voltage, present, take a trip speed, electrode angle, and protecting gas flow rate that directly affect the welding process. These criteria need to be very carefully adjusted based upon the kind of product being welded, its thickness, and the welding method utilized.
Correct welding parameters make sure the ideal amount of warm is put on melt the base steels and filler product consistently. If the specifications are established expensive, it can cause extreme warmth input, creating distortion, spatter, or burn-through. On the other hand, if the specifications are as well low, insufficient blend, lack of penetration, or undercutting might happen.
Top Quality Assurance in Welding Operations

Conclusion
In verdict, mastering the art of welding requires a thorough understanding of undercut welding, its causes, and techniques to prevent it. By making certain proper welding parameters and carrying out see quality guarantee methods, remarkable fabrication results can be attained. It is important for welders to constantly pursue excellence in their welding operations to prevent undercut concerns and generate top quality welds.
Undercut welding, an usual problem in welding processes, occurs when the weld steel does not appropriately fill up the groove and leaves a groove or depression along the bonded joint.To prevent undercut welding, welders need to ensure correct welding specifications, such as readjusting the existing, voltage, travel speed, and keeping the appropriate electrode angle. Poor welding wrong or existing welding speed can also contribute to damage.To minimize the threat of damaging in welding, welders can employ calculated welding strategies aimed at improving the top quality and stability of the weld joints.In conclusion, grasping the art of welding calls for a detailed understanding of undercut welding, its reasons, and methods to avoid it.